Integration between Ongoing WMS and Inventory Planner
Are you working with a sales forecasting system and consider adopting a Warehouse Management System (WMS) alongside it? Or working with a WMS and looking to add a sales forecasting system to the mix? Either way, Ongoing WMS with the Inventory Planner integration could be the choice for you! You’ll be powered by features from the WMS such as batch-picking, getting efficient picking routes, device-agnostic scanning to minimize errors, automatic label printing, bulk product editing, and many more. And with Inventory Planner functionality at your fingertips, you’ll be able to accurately forecast demand and optimize your purchases accordingly. The integration will deliver purchase orders from Inventory Planner directly to Ongoing WMS, based on real sales and article data.
Moreover, if your logistics is outsourced to a 3PL, or if you are 3PL looking for a reliable WMS, know that adding the Inventory Planner functionality to Ongoing WMS is super easy through this integration. Onboarding new customers to your warehouse is in general a breeze when working with Ongoing WMS due to our extensive integration library with 150+ integrations.
Get started with your FREE trial of Ongoing WMS and Inventory Planner today!
Table of contents
Get Started
To activate and use the integration to Inventory Planner the following setup and information is necessary.
- To start generating inventory predictions Inventory Planner will need information about your sales and articles. This information can currently be provided either through an integration to one of the web shops mutually supported by Inventory Planner and Ongoing WMS or by CSV/Excel file exports and imports.
- API key and Account Id of your Inventory Planner system. This information can be found in your Inventory Planner account, at Account ⇒ Settings ⇒ API. For further information see the Inventory Planner help pages or contact Inventory Planner.
When you have this information go to Administration->Integrations, choose Inventory Planner in the list and fill in the necessary information.
Scheduled functions
The integration consists of the following functions which run on a scheduled basis. The scheduled processes can be independently switched on or off to match the expected functionality.
Sync purchase orders
Purchase orders are read automatically from Inventory Planner to Ongoing WMS after creation in Inventory Planner. Ongoing WMS will try to match the Vendor field of an Inventory Planner purchase order with an already existing supplier. If no such match can be found a new supplier will be created and linked to the purchase order.
Field mapping
Ongoing WMS field name | Inventory Planner field name |
---|---|
Purchase order info ⇒ Goods owner order number | Purchase order ⇒ ID |
Purchase order info ⇒ Reference number | Purchase order ⇒ Reference |
Purchase order info ⇒ In date | Purchase order ⇒ Expected date |
Purchase order info ⇒ Order date | Purchase order ⇒ Created date |
Purchase order info ⇒ Supplier | Purchase order ⇒ Vendor |
Purchase order line ⇒ Article number | line ⇒ Sku |
Purchase order line ⇒ External order line ID | line ⇒ ID |
Purchase order line ⇒ Article name | line ⇒ Title |
Purchase order line ⇒ Number of items | line ⇒ Replenishment |
Filters
By default, all orders that have been created in the last 15 minutes in Inventory Planner are synced to Ongoing WMS. Note that only orders with status Open will be synced to Ongoing WMS.
Report purchase orders
Purchase orders are automatically updated from Ongoing WMS to Inventory Planner when they have been received and processed.
Field mapping
Ongoing WMS field name | Inventory Planner field name |
---|---|
Received purchase order line ⇒ External order line id | Item ⇒ ID |
Received purchase order line ⇒ Received number of items | Item ⇒ Received |
Filters
By default, all orders that have been updated in the last 15 minutes in Ongoing WMS is synced to Inventory Planner. Note that only orders that have been processed in Ongoing WMS and are in status Received (or Deflection) will be reported back by default.
Companies using this integration
Some of the companies using the integration between Inventory Planner and Ongoing WMS:
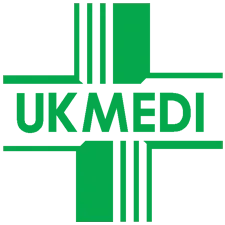
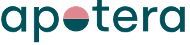