Introduction to returns in Ongoing WMS
Table of contents
Introduction
Handling returns from customers is often a time-consuming process. Ongoing WMS has efficient ways of handling parcels which have been sent back to the warehouse. Each return is registered in Ongoing WMS, and the goods are returned to stock or discarded depending on the cause of the return. Every transaction is tracked, and the information is available directly for further action.
There are different processes for handling returns in Ongoing WMS. For B2C (Business to Consumer), returns will generally be connected to the sales order, while B2B (Business to Business) returns will generally be handled as a purchase order. This page presents an overview of the alternatives.
B2C returns
There are two ways of handling B2C returns in Ongoing WMS, either on the sales order in Ongoing WMS or by return orders. Common for these ways are the traceability to the original sales order and a possibility to set a return cause on each product, data that can be used to evaluate products and map customers behavior.
Return causes
There are usually several return causes specified on the return form sent with the order to the customer. To be able to add this information in the system when processing the return on the sales order, these return causes need to be set up in a goods owner specific register in Ongoing WMS.
The return cause list is found at the register menu
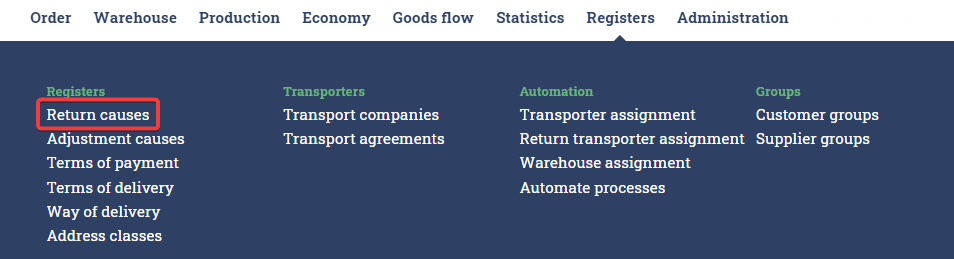
Click Create new return cause
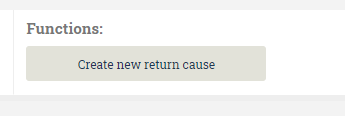
Add the names, that matches the alternatives used on the return form, and set a code.
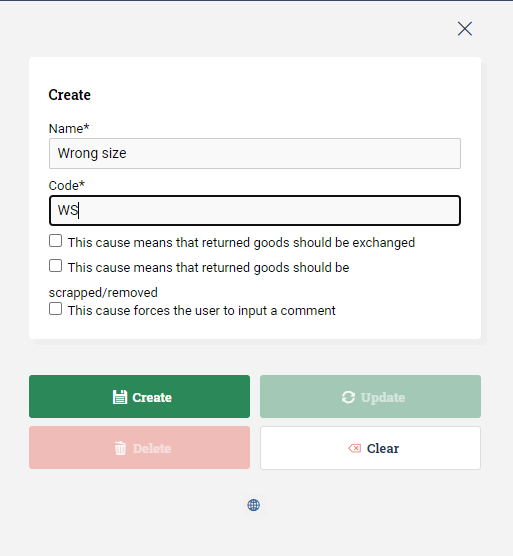
When the list is complete the returns can be registered on the sales orders with the correct return cause.
When using a Return Management System (RMS) system, this return cause list are usually created by the integration, since the causes are added when return orders are synced to Ongoing WMS. The list of all alternatives can still be found at this return cause menu.
Process returns based on the sales orders
In this case, the order is returned to the warehouse without having been advised. When the items have arrived back at the warehouse, the return is processed using the original sales order in Ongoing WMS. This can be done either manually in the order list or in the scanning module.
When processing the return, set a return cause and then choose to either put the items back in stock, or discard (scrap) them.
When the return has been fully processed, it can be reported to ERPs or a notification can be sent by email to the goods owner.
Please see our guide on how to process a B2C return in Ongoing WMS.
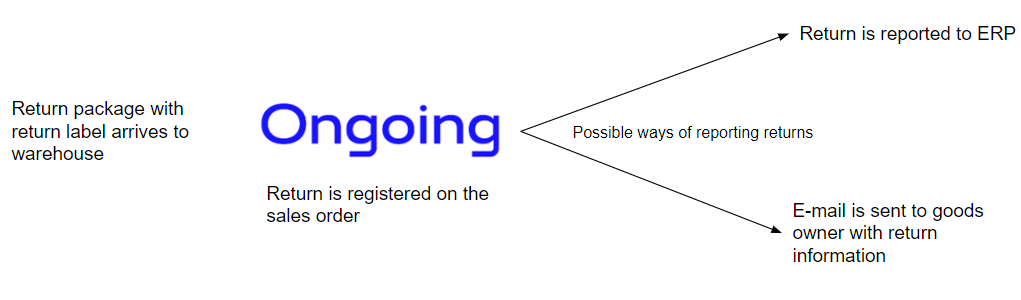
Working with advised returns using return orders
Return Merchandise Authorization (RMA) is in Ongoing WMS implemented using return order. It is a way of advising the warehouse about an incoming return and add extra information to it. This process can be done manually in Ongoing WMS, through integration to RMS or as part of a bigger integration to an ERP. Read our guide about how to work with these orders here.
Use an integrated Return Management System
If the goods owner uses an RMS, returns are generally advised to the warehouse by the WMS. Each return appears as a return order in Ongoing WMS. The return orders are used to process the return when the package arrives at the warehouse.
At our integrations page you can see which services have integrations with Ongoing WMS today.
When the return has been finished in Ongoing WMS, it is reported back to the RMS.
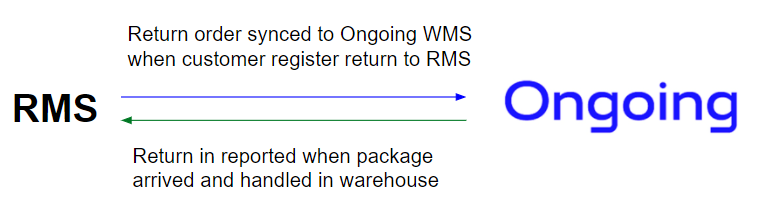
Video on how to handle return orders in Ongoing WMS and putting them back into stock using a cart
B2B returns
When B2B orders are returned, they are usually handled in Ongoing WMS as regular purchase orders. If you have an integration with an ERP system, the purchase orders may be generated in the ERP. Otherwise, you may create the purchase orders manually in Ongoing WMS.
It is possible to distinguish this kind of purchase order from an ordinary purchase order, by using the Return parameter.
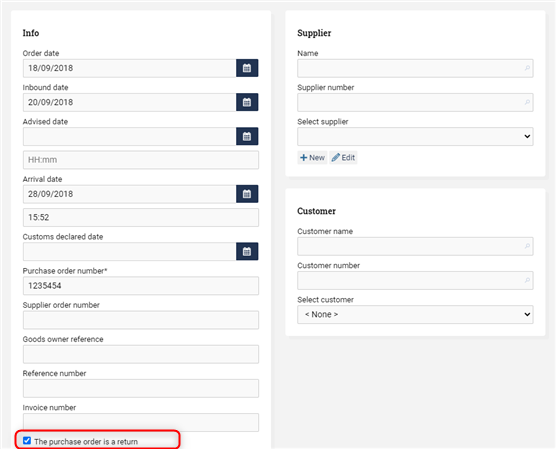
This kind of purchase can be processed exactly like any other kind of purchase order. Please see our guide for more information about processing purchase orders..